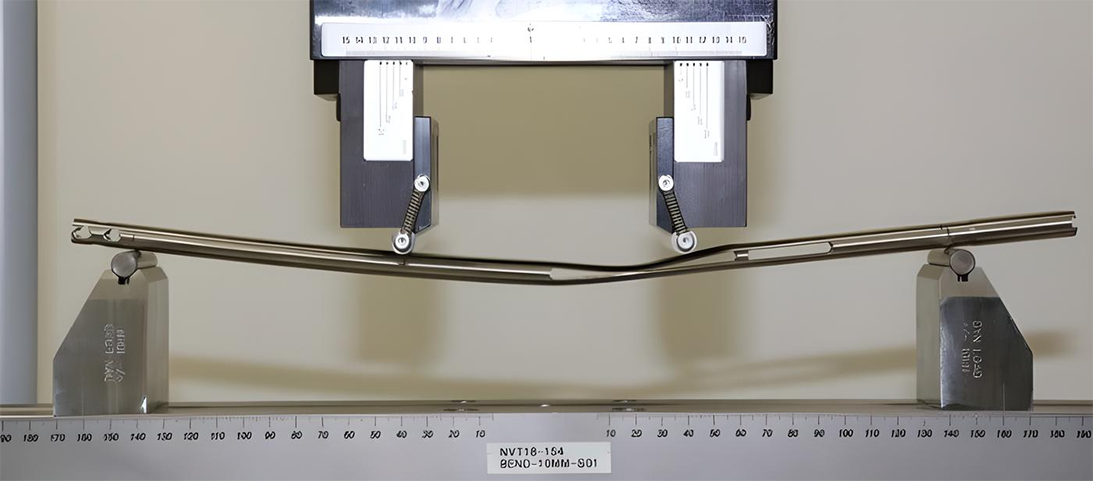
The internal environment of living organisms proves a harsh milieu for manufactured items due to the corrosive ions that break down most materials. Only a few strong metals have demonstrated biocompatibility over the long term when utilized to create medical devices such as orthopaedic implants. These include certain stainless steels, some cobalt-chrome alloys, and titanium and several of its alloys, along with a limited number of other substances. Likewise, when complex electronic components are essential to a device’s function (as with implantable pacemakers), these elements must be durably sealed from contact with bodily fluids and tissues. Rather than spending time and resources testing unique metals for biocompatibility, orthopaedic implant manufacturers typically start with materials that have a proven track record for safety and longevity and shape those materials for implant use.
Regulatory background
The 1967 Medical Device Regulation Act (MDRA) authorized the FDA to supervise the manufacturing, distribution, and sale of medical devices. The MDRA created three classes of medical devices reflecting progressively increased risk to patients using the products. For example, bedpans and bandages are Class 1 devices, whereas syringes and blood pressure cuffs fit into Class 2. By their very nature, orthopaedic implants are typically Class 3 devices because of the danger involved with their insertion and usage. Thus, they require FDA pre-market approval before sale to the public.
In 1990, President George H. W. Bush enacted an amendment to the MDRA that requires collection of post-marketing adverse event data to ensure that medical devices function as intended. People in the medical device industry realize that they or a loved one might someday find themselves in a far-off town’s emergency room, hearing an on-call surgeon request consent to insert a product into their body to preserve life or limb—high motivation, indeed, to produce high-quality implants.
Testing metallic implants
From an engineering perspective, it is important for orthopaedic surgeons to understand all the forces exerted on an orthopaedic implant by patient activities of daily living and then simplify the mechanical system into a testable configuration. Thereafter, the job is straightforward: Ensure that activity loads do not exceed the limits of the device. Fortunately, there are typically pre-existing (“predicate”) devices with known clinical histories that can eliminate the need for testing of many possible loading conditions. Furthermore, ASTM International (formerly the American Society for Testing and Materials) and the International Organization for Standardization (ISO) have established standards for this purpose, although with this cautious disclaimer: “This test method is not intended to define case-specific clinical performance of these devices, as insufficient knowledge to predict the consequences of the use of any of these devices in individual patients is available.”
The biomechanics of gait activities are complex, with combinations of bending loads under both compression and tension, along with sheer and torsional forces. Even when attempting to evaluate the wear characteristics of a product, there is no need to exactly replicate the stress profile of the device through full range-of-motion testing. Instead, simplified tests set to the highest magnitude of force in the correct vector during activity will suffice. Finite element analysis is used to estimate peak stresses under such forces and come up with experimental designs to quickly simulate the pertinent loads, allowing for rapid design iterations and optimization prior to physical testing. These forces are applied to the implant by powerful testing machines, typically stressing the implant to failure.
Assessing an intramedullary nail
As an illustration, consider the testing required for a new intramedullary nail that incorporates a slot on both sides along its length to allow for bone transport. The ASTM F1264 requirements for intramedullary nails specify bending and torsion testing, because these are the likely loads placed on the device during implanted use. Computer-generated simulations first “stress” the potential implant with four-point bending loads, followed by actual mechanical testing to failure in a four-point bending machine and final testing in a biomechanical configuration (Figs. 1 and 2).
Although failure mode for static loading is predictable, it is just as important to test devices under repeated cyclical loading, as orthopaedic implants are intended to withstand repeated loads from patient weightbearing. Failure modes from fatigue testing of implants can be different from those observed in static loads. Fatigue cracking propagation starts in areas of high stress concentrations. For example, corners of internal or external step transitions, threads, and especially welds yield first. Evaluation of torsional strength is conducted in the same way: first, computer simulation to drive design iterations and optimization, then physical testing to failure.
In the above example, these tests determined that the bone transport implant’s original design was insufficient to create a product strong enough to withstand stresses placed upon it during daily patient use. Therefore, the product returned to the design team, who added a small metal bridge across the slot on both sides of the nail. Repeat testing demonstrated that the device met all design requirements, and an application was submitted to the FDA for marketing approval.
Applying the aforementioned principles of orthopaedic biomechanics, implant manufacturers working with surgeons and engineers have created medical devices that have improved the quality of life for countless patients around the world.
Emmon Johnny Chen, MS, is an engineer with more than 13 years of diverse experience in orthopaedics, specializing in the design and development of medical implants for trauma, arthroplasty, limb lengthening, and limb salvage.
References
- ASTM International: Standard Specification and Test Methods for External Skeletal Fixation Devices. Available at: https://www.astm.org/f1541-17.html. Accessed March 11, 2024.
- ASTM International: Standard Specification and Test Methods for Intramedullary Fixation Devices. Available at: https://www.astm.org/f1264-16e01.html. Accessed March 11, 2024.